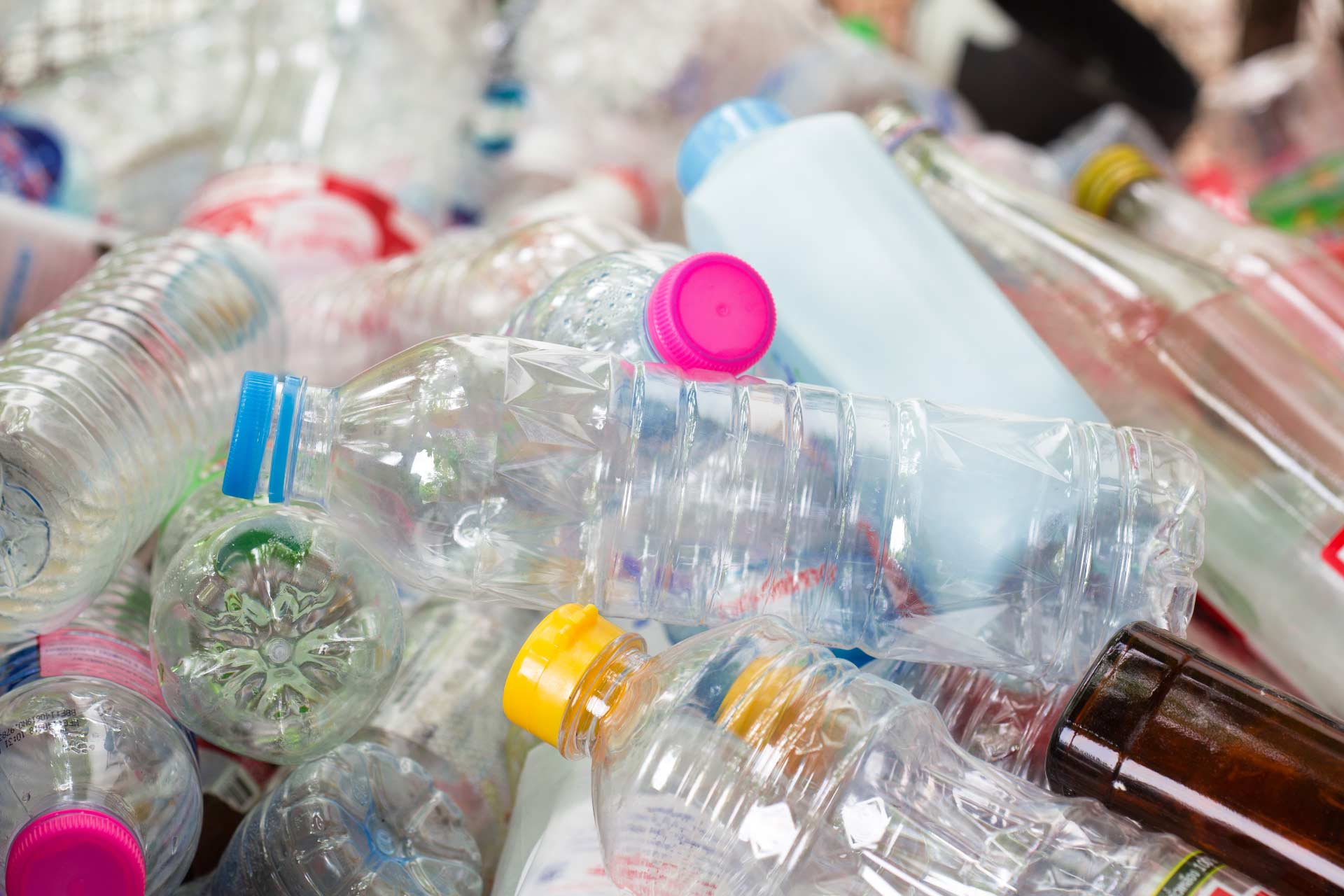
With plastic pollution as the focus of this year's Earth Day, we take a closer look at a three-year multi-disciplinary project by our Operations and Supply Chain Management (OSCM) experts, aimed at addressing the challenges of producing more sustainable plastic packaging for fast moving consumer goods (FMCG).
Professor Andy Lyons, Dr Gopal Narayanamurthy and Dr Kostas Tsiamas are working with colleagues from University of Manchester, Unilever and IPL Brightgreen, on a framework to better understand how packaging manufacturers can increase the proportion of recycled resins without affecting the quality and performance of the resulting products, as well as the challenges involved in developing circular supply chains for recycled plastics.
As part of this combined effort, they will assess the economic, social and environmental impact, and viability of more circular supply chains, which use a higher proportion of recycled plastic in the production of packaging for day-to-day consumer products.
The goal is to develop a framework which explains the implications of increasing plastic circularity for FMCG’ plastic containers.
This is a Natural Environment Research Council-funded project, aimed at enabling innovation in the production of smart, sustainable plastic packaging for FMCGs, and reducing plastic pollution by 2025 through cleaner supply chains.
A business case for more sustainable plastic packaging
According to one of the most recent Government reports on plastic waste, approximately five million tonnes of plastic are used in the UK every year, nearly half of which is packaging. From this, around 50% is subsequently recycled, with the remainder going to landfill, energy recovery (ie incineration) or ending up in our natural environment.
Most common plastics used in packaging come from petroleum resins that take hundreds of years to degrade, a lifespan that far exceeds the functionally required for day-to-day products.
As a result, the relentless accumulation of plastic waste increases the pressure on the packaging industry, to try and find economically viable ways to reduce, reuse and recycle existing plastics.
While plastic pollution is one of the greatest global environmental challenges, thermoplastics are fantastic materials, with multiple applications in the packaging industry, due to their low weight, strength and durability.
Cost-effectiveness, food-safety and transportation advantages, are the reasons behind the omnipresence of thermoplastics in our day to day lives, from milk bottles to shampoo and detergent containers.
The majority of plastics used in packaging can be recycled and legislators are driving change towards eco-friendlier ways to repurpose post-consumer recyclates (PCR) through economic incentives.
For example, in the UK the new ‘Plastic Packaging Tax’ requires companies that manufacture or import 10 or more tonnes of plastic packaging per year, to pay over £200 per tonne.
However, the tax does not apply to businesses whose packaging contains at least 30% recycled plastic, reinforcing the need for initiatives to create smarter and more sustainable plastics.
Not an easy challenge
Replacing a large proportion of virgin plastic with PCR, would be a big step forward in increasing the sustainability of plastic packaging.
However, with recycled resins often being more expensive than virgin plastics in Europe, manufacturers and buyers face an important financial barrier.
Alongside higher production costs, formulating high-performing plastics with recycled feedstocks presents a formidable challenge, because an increase in PCR content typically reduces performance, limiting the use of the resulting packaging.
Previous work with Unilever indicates that the chemical and mechanical properties of packaging materials depend on the amount and quality of the recylates included in the formula.
Currently, mechanical recycling is the only economically viable method for regenerating the most commonly used types of synthetic resins, such as polyethylene terephthalate (PET) and high-density polyethylene (HDPE).
However, petroleum resins cannot be reprocessed infinitely, as the elevated temperatures plastics are exposed to during the recycling process break down the polymer chains, compromising the quality and performance of the resulting product.
While fillers and additives can help offset performance issues, further research is needed to inform decisions on the correct mix and quantity of additives needed for products with a larger proportion of recyclates.
In addition, batches of recycled plastic are typically subject to limited characterisation on levels of degradation, odour, fouling, etc, which means there is little information to predict its behaviour and the quality that can be delivered to the end user.
These factors reduce flexibility in the market, increase the cost for PCR incorporation and ultimately place an economic penalty on businesses that try to produce and use more sustainable plastics.
Therefore, the effective incorporation of PCR into packaging requires a significant optimisation of the final product and a trusted relationship between the supplier and the buyer.
Understanding the Circular PCR supply chain
In order to respond to the strategic challenges of producing and selling more eco-friendly plastic packaging, Andy, Gopal and Kostas are investigating the economic and environmental footprints of the cyclical PCR supply chain across six key players:
- Local authorities - post-consumer waste collection
- Materials recycling firms - manual sorting and baling
- Plastics recycling firms - crushing and washing
- Plastic/oil firms - virgin plastic pellet production
- Speciality chemical firms - antioxidant production and additive compatibilising
- FMCG firms - recycled plastic transformation into usable products and service provision to consumers.
Their research aims to address several key challenges, by modelling potential disruptions to the supply chain.
As the first five players operate within a business-to-business (B2B) setting, a significant challenge for the efficient functioning of the supply chain is maintaining PCR demand circularity with different independent actors involved.
With seven different unique plastic types available based on their resin type1, another key challenge to tackle is how to maintain a supply of particular grades, when most recovered plastic from domestic streams comes as a mixture of different polymers and colours.
Alongside this, through the implementation of additives, recycled materials can be produced from a blend of plastic grades, but research on how to chemically break down mixtures of plastics is still ongoing.
When these used products re-enter the supply chain for recycling, sorting them into specific grades presents significant issues, impacting the availability, affordability, and acceptability of PCR grades and their products, via the players in the supply chain.
To address these problems, they are developing a profiling framework as part of the research project, to analyse how the use of different configurations of recycled plastic perform.
The final framework will allow researchers to map results against financial, social and environmental scenarios, depending on changes in demand and supply, to fully understand the business case for using additives.
In addition, the framework is expected to help assess the implications of government environmental policies, including the newly introduced ‘Plastic Packaging Tax’.
The ultimate goals of the project will be defining industry-led quality standards for PCR, increasing the use and market value of recycled plastics and providing a standardised set of tests to allow PCR manufacturers to test and grade their materials.
1 Plastics are classified according to their resin type into: Polyethylene Terephthalate (PET), High Density Polyethylene (HDPE), Polypropylene (PP), Polyvinyl Chloride (PVC), Low Density Polyethylene (LDPE) and Polystyrene (PS)
Professor in OSCM and Head of the OSCM Subject Group |
|
![]() |
Dr Gopalakrishnan Narayanamurthy Senior Lecturer in OSCM |
![]() |
Postdoctural Research Associate |